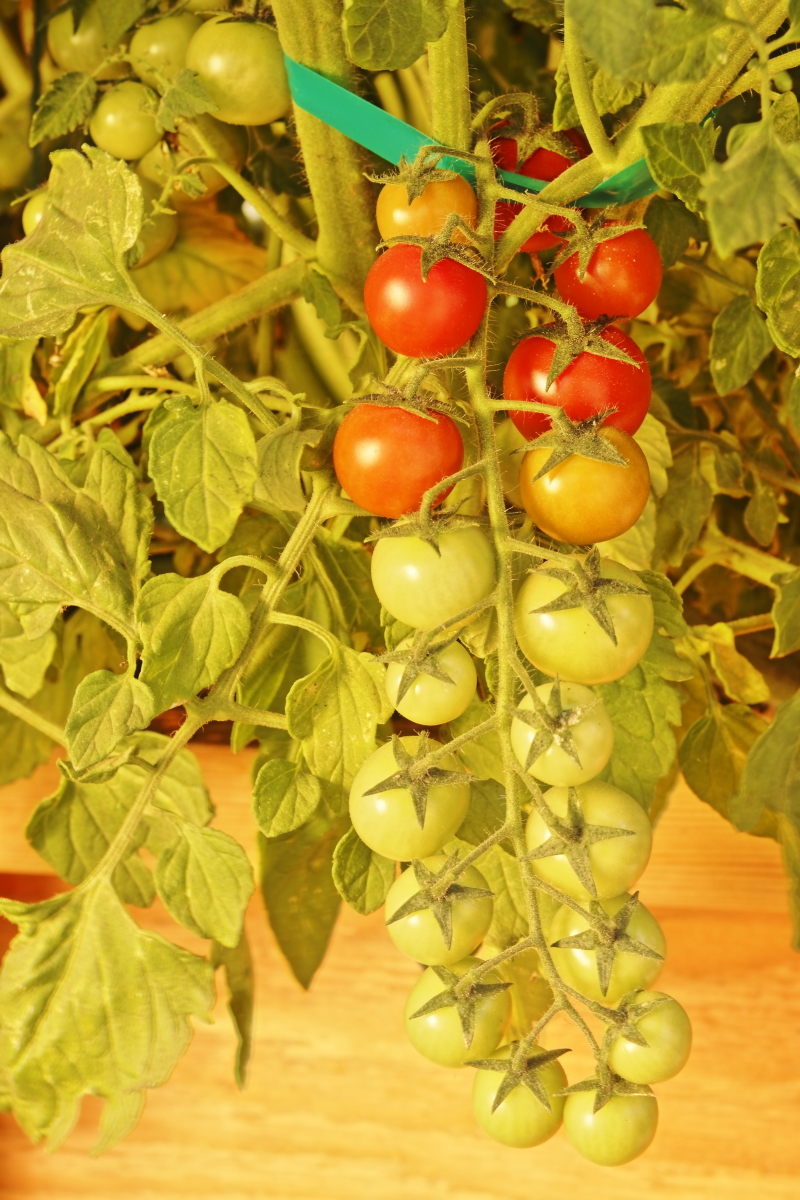
I want to illustrate the benefits of systematically optimizing a process, to encourage you to optimize all the key factors in your production process, by conducting process experiments according to efficient designs, for example the two factor, two level factorial design, among others.
I believe that’s what Dutch tomato farmers have been doing for quite some time now. After all, there are dozens of factors to optimize in tomato production. When it comes to productivity, Dutch farmers are the best on the planet.
Let’s take a look at some of the factors they’ve optimized regarding tomato crops. I’m confident this brief overview will inspire you to apply a similar approach to your production process.
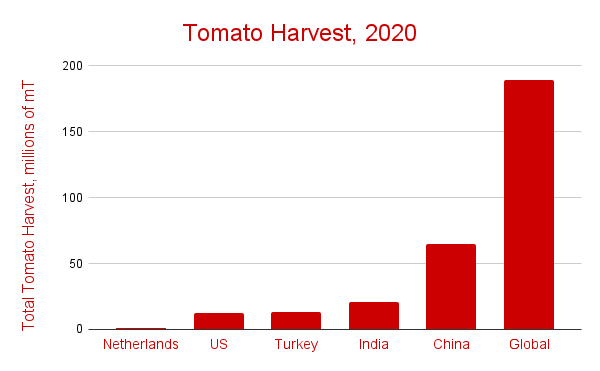
The Global Context for Tomato Crops
Globally, 189 million metric tons of tomatoes were produced in 2020, growing annually by 2%. The top producers were China, India, Turkey and the US, whose total harvests were 64.8, 20.6, 13.2 and 12.2 million metric tons, respectively, accounting for more than half of global production. So we can regard their numbers as relevant to the state of the art for growing tomatoes.
What’s interesting to the experimenter is the enormous variation in the productivity for growing tomatoes on a given area of land. In 2020, the productivity for the top four producers, in metric tons per hectare, was 58.4, 25.3, 72.6 and 110.7, for China, India, Turkey and the US, respectively. The global average was 37 metric tons per hectare. Notice that the productivity varies by more than fourfold.
Now consider the Netherlands. While they only produced 0.9 million metric tons, their productivity was 486.6 metric tons per hectare, more than ten times the global average. That’s 48.7 kg of tomatoes per square meter! Moreover, some greenhouses in the Netherlands report productivity up to 80 kg per square meter.

How did Dutch farmers take such a huge lead in crop productivity?
The Dutch have optimized a whole slew of factors affecting tomato growth, quality and yield. Their efforts extend to agricultural research, horticulture, greenhouse and hydroponics technology, and the strategy with which they organize their supply chain infrastructure. They also foster collaboration and knowledge transfer between farmers, researchers, customers and industry stakeholders. Clearly, the Dutch have left no stone unturned in optimizing their tomato production.
Greenhouse Factors
They’ve optimized the temperature, airflow, humidity, lighting, and carbon dioxide concentration in their tomato greenhouses. They’ve come up with several innovative engineering solutions to control airflow, temperature and humidity within their greenhouses. They control both the intensity and uniformity of sunlight on their crops by equipping their greenhouses with diffusers, reflectors and shade baffles. They even equip their greenhouses with artificial lighting, for which they’ve optimized the color spectrum by making use of high output LED lights. They enrich their greenhouse atmosphere with carbon dioxide up to 1000 ppm, more than twice the ambient level.
Hydroponic Irrigation Factors
They’ve replaced garden soil with hydroponics, to continuously control the nutrients fed to their crops. That means they can optimize the recipe for the growth solution in terms of pH, calcium, N-K-P and so on, then adjust it throughout the lifecycle of their crop, through plant growth, flowering, fruit growth and ripening stages.
They’ve also optimized the substrate materials for supporting the roots of their tomato plants as they grow in the hydroponic broth. They’ve found lightweight blocks of rock wool to perform the best.
More recently, they’ve optimized how to recirculate and replenish their hydroponic solutions, to conserve water and make their greenhouses self-sufficient. Typically, they can use four times less water to produce a kilogram of tomatoes than a crop grown in soil.
Automation and Robotics Factors
The Dutch lead the way in robotics for planting, harvesting and monitoring their tomato crops. That means they can respond to germination,plant growth, flowering, fruit growth and ripening stages of their crops in real time. The rewards must be well worth it in terms of ROI, for them to resort to advanced robotics and automation, to control all the time-sensitive factors relevant to tomato crops.
Horticulture Factors – Tomato Plant Variety
The Dutch are no slouches when it comes to optimizing their tomato varieties. For example, the Duijvestijn greenhouses test 200 new varieties every year. They focus on varieties that grow vertically to suit the space constraints of their greenhouses and to facilitate their harvesting operations. They’ve optimized these varieties to boost productivity while yielding the best selling fruit over the longest harvest period.
The key factors for best selling fruit include size, shape, color, brix level, sweetness, tartness, mouthfeel and shelf life. Of course the Dutch account for these factors in their tests and experiments towards optimizing their tomato varieties.
By grafting cuttings onto root stock, they’ve also optimized the variety of tomato root stock to suit their hydroponic operations.
Are the Counter Arguments to Maximum Productivity even Relevant?
In a word, no.
But let’s consider the counter arguments, for sake of argument.
Critics of the Dutch, the Tomato farmers outside the Netherlands, argue that the extraordinary crop productivity achieved by the Dutch comes at the cost of flavor and quality. They also argue that the ultimate depth of flavor arises from the soil, similar to the way a fine vintage of wine relies on the terroir of the vineyard. For proof, these critics cite the much higher prices fetched by their soil grown crops.
But the Dutch have chosen to optimize for the productivity and bestselling properties of their tomato crops. They’ve also chosen to optimize water and energy consumption. The thing is, they can also choose to optimize for flavor, texture and other characteristics, as they see fit. At the moment, they appear more intent on the bottom line, the ROI for their crops.
At the moment, there appears to be a trade off between ultimate flavor and productivity. But I’m sure that consistent, persistent testing and experimenting will inevitably crack that nut in the Dutch farmers’ favor.